8 European Organisations look into improving accuracy in setting up big and heavy raw part components in machine tools
Funded by the European Union and the EIT Manufacturing, the recently started TACCO Project seeks the development of a groundbreaking innovation for the fast, reliable and accurate set-up of raw parts using an attractive, flexible and easy-to-use modular approach based on photogrammetry.
Under the Zero-Defect manufacturing goal, the machining of medium and big size parts with the required and suitable accuracy is a challenge, especially in high added value products manufactured in small or single-unit batches made of high performance materials like in aeronautic, space or energy sectors.
Initial set-up of such parts at the machine is a critical process, as the excess material of the raw part (overstock) with respect to the final part must be distributed at all the surfaces to be machined. Incorrect fixturing and location would give rise to spoiling the part, with a very high money loss. Due to the high cost (money, energy, and time) associated with the rejection of a part, the initial alignment is done by long time-consuming processes (mostly manual). Several approaches exist, all of them having a certain part of the process being performed on the machine itself. This accurate process is labor intensive and strongly dependent on skilled operators using specialized measuring instruments (e.g.: laser-trackers) and metrological software, usually performed in a nonrepetitive way (part specific process and tooling), with high risk of error. As a result, this critical process still remains far away from its optimal, limiting the competitiveness of the manufacturing of large components.
To overcome these set-up process limitations, TACCO Project aims at developing a groundbreaking innovation for the fast, reliable and accurate set-up of raw parts using an attractive, flexible and easy-to-use modular approach based on photogrammetry, enabling the democratic engagement of one-of-a-kind operators to a critical manufacturing process step, the raw part set-up, that stills remains kidnaped and limited to experienced operators and specialized tools. TACCO system will be the ground-breaking upgrade of a predecessor beta system by SORALUCE, the so called VSET(https://www.soraluce.com/en/vset) already validated at lab environment and first industrial beta-users. To keep informed about the news, results, and events you may join the TACCO community of stakeholders through the main social media or e-mail jbilbatua@mondragoncorporation.com
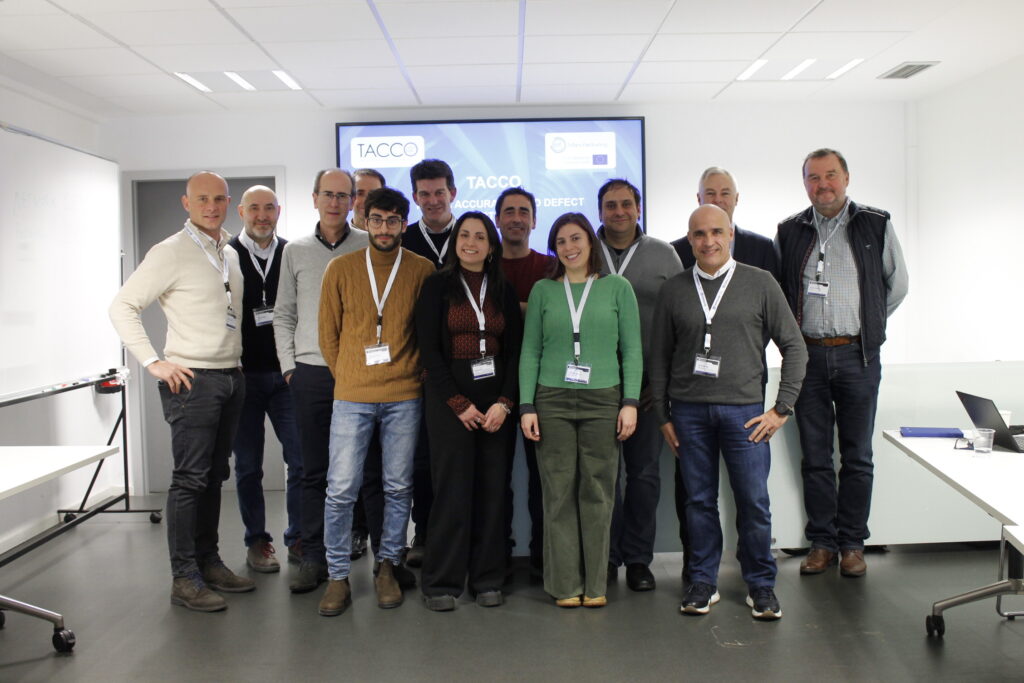
TACCO Kick offs at SORALUCE’s facilities in Osintxu, Basque Country, Spain
Leaded by MONDRAGON Corporation, and with the presence of 3 business owners SORALUCE, MATZAT and RENISHAW, the research center IDEKO and the Politecnico di Milano, the TACCO consortium met together last 24th and 25th January 2023 at SORALUCE’s facilities in Osintxu, Spain.
Partners have the chance to review the overall status of the project through the different planned sessions that were chaired by joseba Bilñbatua (MONDRAGON Corporation). Discussion focused on WP1 (Technical specification of industrial use cases by BBM and WWR, and WP6 Dissemination, communication and exploitation and WP7 Project Management.
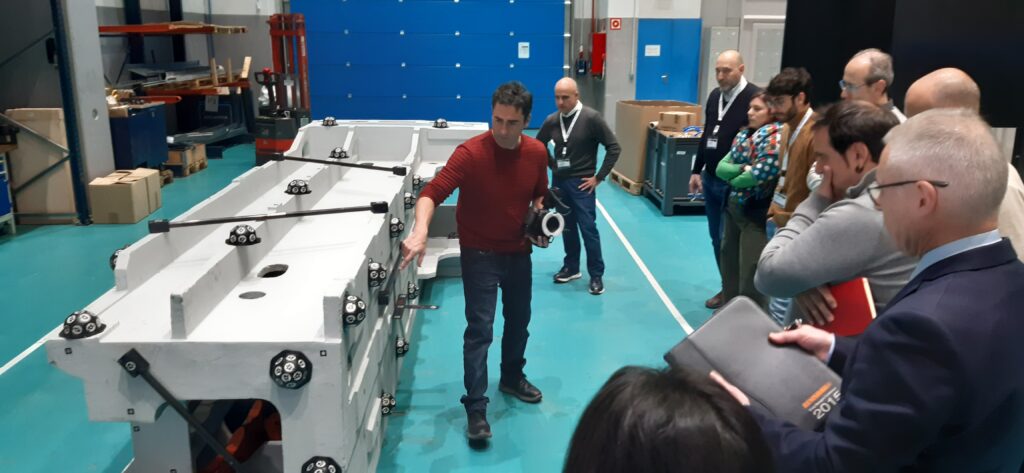
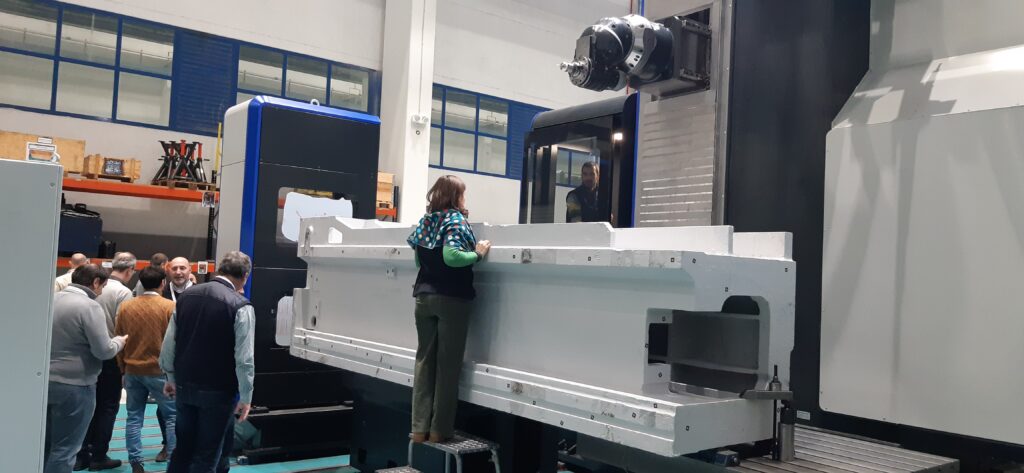
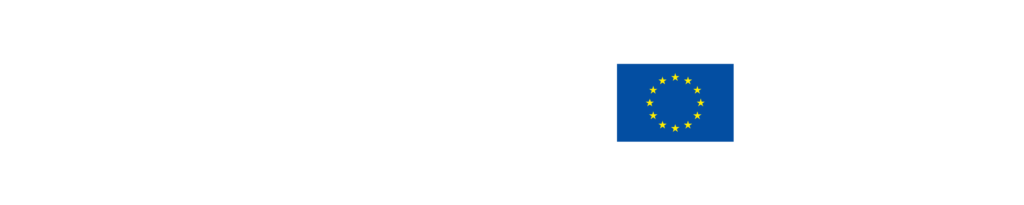
«Funded by the EIT Manufacturing and the European Commission. Views and opinions expressed are however those of the author(s) only and do not necessarily reflect those of the EIT Manufactuing nor the European Union or the European Health and Digital Executive Agency (HADEA).»